Sabbiatura Metalli: cos’è e vantaggi
La sabbiatura dei metalli è una delle tecniche più efficaci di preparazione e trattamento dei manufatti per garantire durabilità e qualità delle superfici nelle successive lavorazioni (verniciatura, saldatura ecc).
Con l’utilizzo dei metodi appropriati e la scelta adeguata degli abrasivi, la sabbiatura può essere eseguita in modo sicuro, efficace, ed economico, vediamo come.
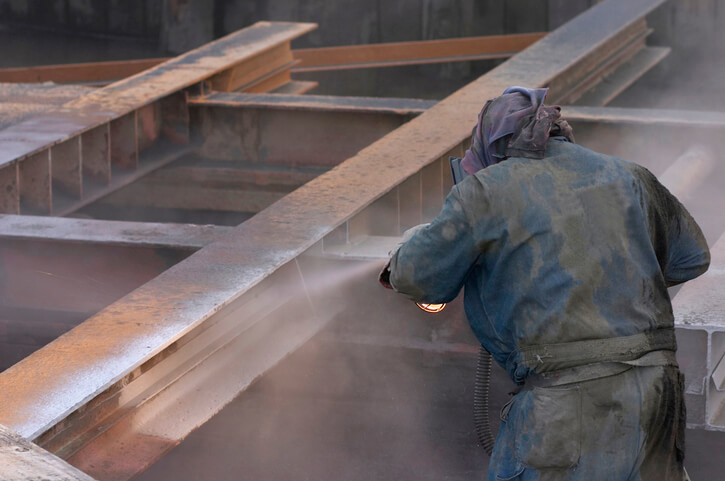
Cos’è la sabbiatura
La sabbiatura è un processo di lavorazione che consiste nell’irrorare una superficie metallica mediante getto ad alta pressione di acqua o aria e materiale abrasivo (solitamente sabbia), rimuovendo impurità, calcificazioni e ruggine.
Nel contesto della produzione industriale, la sabbiatura rappresenta dunque una fase intermedia essenziale, durante la quale la superficie del pezzo viene preparata per le operazioni successive, di solito verniciatura o saldatura. Durante questo processo, il pezzo viene completamente pulito e la sua superficie assume una rugosità ed omogeneità che dipendono dalla dimensione dei granuli di sabbia utilizzati e dalla pressione del getto.
In particolare, la sabbiatura dei metalli permette di eliminare:
- impurità (macchie di olio o grasso)
- ruggine
- vecchie vernici e altri residui
Non solo metalli…
Tra i materiali idonei alla sabbiatura come legno, vetro, plastica e ceramica, i metalli trovano ampia applicazione.
Acciaio, ferro, alluminio, ottone, rame, titanio, ghisa e altre leghe riescono a raggiungere un grado di rifinitura, lucidità e uniformità superficiale tali da rendere la sabbiatura largamente impiegata in settori come l’industria metalmeccanica, dell’automotive, del restauro e della conservazione e dell’edilizia.
Sabbiatura metalli: quando e perché farla
La sabbiatura offre una serie di vantaggi significativi, soprattutto quando si tratta di pulire superfici complesse e difficili da raggiungere, come angoli, insenature e spigoli. Questo la rende ideale per componenti meccanici come motori, riduttori di giri e ingranaggi, dove la pulizia accurata è fondamentale per il corretto funzionamento.
I vantaggi della sabbiatura: perché farla
La sabbiatura rappresenta un processo essenziale nel trattamento delle superfici metalliche, offrendo una serie di vantaggi significativi che contribuiscono alla qualità e alla durabilità dei manufatti.
Di seguito esamineremo in dettaglio i principali vantaggi della sabbiatura per metalli:
- Omogeneità della pulizia
- Omogeneità della superficie
- Adattabilità al materiale
- Benefici nelle successive lavorazioni
Il processo di sabbiatura: macchine e grani
Durante il processo di sabbiatura, i granuli abrasivi vengono proiettati sulla superficie metallica tramite una pistola o un ugello a pressione controllata.
La sabbiatura può essere eseguita utilizzando diverse tipologie di granuli abrasivi e macchine sabbiatrici, a seconda del tipo di superficie e delle esigenze specifiche del trattamento.
Le macchine sabbiatrici
Le macchine sabbiatrici sfruttano la pressione dell’aria compressa per proiettare polveri abrasive sulla superficie da trattare. Esse sono composte principalmente da un serbatoio contenente l’abrasivo, un tubo di trasporto e un ugello di sabbiatura. La pressione dell’aria compressa varia solitamente tra i 6 e gli 8 bar, e il consumo di aria può variare dai 200 ai 1000 litri al minuto, a seconda del tipo di macchina e dell’ugello utilizzato. Maggiore è la dimensione dell’ugello (da 4mm a 8mm), maggiore sarà la richiesta di aria.
Il principio di funzionamento è abbastanza semplice: l’aria compressa spinge le polveri abrasive attraverso l’ugello, che vengono poi dirette verso la superficie da trattare.
Le differenze di pressione e volume d’aria influenzano la velocità e l’efficacia del processo di sabbiatura. Le macchine possono essere regolate per adattarsi a diverse esigenze di lavoro, consentendo una maggiore precisione e controllo durante l’operazione.
Le principali tipologie di macchine sabbiatrici sono:
- Sabbiatrice a pistola. Ideale per piccole e basiche esigenze di sabbiatura, simile a una pistola di verniciatura. Ha un serbatoio integrato con un volume massimo di circa 0.9 litri, indicato per lavorazioni su bordi esterni ed interni di componenti come porte, paraurti, piccoli telai o soglie.
- Sabbiatrice a cabina da banco. Composta da una mini cabina posizionabile su un banco di lavoro. L’azionamento può essere comandato tramite pedale o grilletto della pistola. Solitamente dotata di un contenitore di sabbia da 5 a 10 kg, è indicata per lavorazioni su componenti di dimensioni medio-piccole.
- Sabbiatrice a cabina da terra. Indicata per utilizzi medi e professionali, disponibile in diverse grandezze per permettere maggior spazio alle operazioni. Grazie a una porta laterale, consente il caricamento di particolari più pesanti. Alcuni modelli possono essere dotati di aspirazione e relativi filtri per migliorare la visibilità durante le lavorazioni e recuperare meglio la sabbia.
- Sabbiatrice a recupero. Apparecchi mobili progettati per trattenere il materiale abrasivo durante il processo, evitando la dispersione nell’ambiente e consentendo il suo riutilizzo immediato.
- Sabbiatrice modulare. Dotata di un sistema di controllo remoto a doppio comando, sia pneumatico che elettrico, che consente all’operatore di avviare e fermare la macchina e regolare la fuoriuscita dell’abrasivo da una posizione distante.
I grani di sabbiatura
Vengono impiegate varie tipologie di graniglie, tutte costituite da masse inerti di forma irregolare ed angolosa.
La scelta della tipologia di graniglia dipende dalla superficie: all’aumentare della durezza della superficie da trattare, si tende ad utilizzare graniglie abrasive di dimensioni maggiori per aumentare il loro impatto sull’area trattata.
Le diverse graniglie utilizzate includono:
- Graniglia al quarzo (una delle più comuni. Viene utilizzata per la sua durezza e capacità abrasiva. Particolarmente efficace nella rimozione di ruggine, vernici vecchie e impurità dalla superficie dei metalli)
- Abrasive metalliche (hanno un’elevata capacità abrasiva. Sono ideali per la rimozione di residui di saldatura, ossidazione e altre impurità dalle superfici metalliche)
- Microsfere (particelle sferiche di vetro in granulometrie da 40 a 800 micron, acciaio o ceramica, utilizzate per sabbiature più delicate. Sono ideali per la pulizia di superfici sensibili poiché producono un effetto meno aggressivo rispetto ad altre graniglie)
- Granuli plastici (impiegati per la sabbiatura di materiali delicati o sensibili al calore, come plastica o legno. Sono utilizzati per ottenere una pulizia accurata senza danneggiare la superficie)
- Granuli di ghisa o corindone (composti da ossido di alluminio in grana 36 o 80, sono utilizzati per la rimozione di incrostazioni più resistenti e per la preparazione di superfici metalliche prima della verniciatura o della zincatura)
Un’ulteriore classificazioni dei grani li suddivide a seconda del grado di pulizia superficiale ottenuto:
- Sa1 (grossolana o di spazzolatura). La superficie presenta residui aderenti di ruggine, laminazione e pittura.
- Sa2 (commerciale). La superficie risulta pulita e presenta un colore scuro non uniforme.
- Sa2,5 (al metallo bianco). La superficie si mostra completamente priva di impurità e presenta un colore uniforme.
- Sa3 (a metallo bianco più profonda). La superficie appare completamente pulita e uniforme, con una lucentezza in alcuni metalli come il ferro.
Questa suddivisione dei gradi di pulizia si basa sulle norme internazionali, in particolare sulla ISO 8501-1, che fornisce linee guida per la preparazione delle superfici di acciaio prima della verniciatura o di altri trattamenti protettivi.
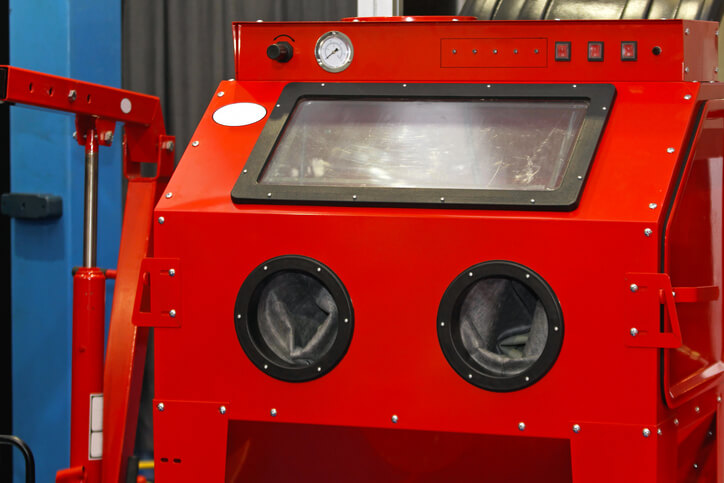
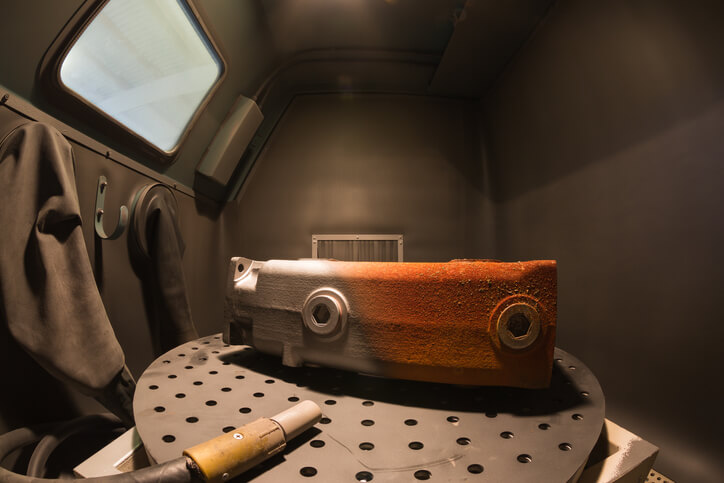
Metodi di Sabbiatura
I principali metodi di sabbiatura sono:
- per via umida
- a secco
e
- convenzionale o a ciclo aperto
- ad aspirazione o a ciclo chiuso
Sabbiatura per via umida
Un vantaggio della sabbiatura per via umida, nella quale viene introdotta acqua o soluzione acquosa nella corrente abrasiva, è la riduzione di polvere prodotta. È utile quando non è possibile eseguire l’operazione in un ambiente aperto o in una cabina dedicata.
Tra gli svantaggi, questo metodo può risultare meno efficace in presenza di recessi o superfici complesse.
In aggiunta, l’inclusione di acqua durante il processo di sabbiatura umida può favorire la formazione di ruggine, nonostante l’eventuale aggiunta di composti antiruggine.
Risulta infine essere più lenta rispetto alla sabbiatura a secco. Questo rallentamento è dovuto al fatto che la presenza di acqua riduce l’efficacia abrasiva del materiale impiegato, aumentando di conseguenza il tempo richiesto per completare il processo. Di conseguenza, i costi di produzione aumentano parallelamente alla durata dell’esecuzione.
Sabbiatura a secco
Questo metodo prevede l’utilizzo di una miscela di aria compressa e sabbia o graniglia abrasiva senza l’aggiunta di acqua. È il metodo più comune e versatile, adatto a una vasta gamma di superfici metalliche.
Sabbiatura convenzionale
La sabbiatura convenzionale, anche nota come sabbiatura aperta, è un metodo di trattamento delle superfici in cui non sono implementate misure specifiche per ridurre i rischi legati alla produzione di polvere né per il recupero del materiale abrasivo.
Sabbiatura a ciclo chiuso o con sistema di aspirazione
Nel processo di sabbiatura a ciclo chiuso o con sistema di aspirazione, sono previste soluzioni per limitare la dispersione della polvere e per recuperare il materiale abrasivo esaurito.
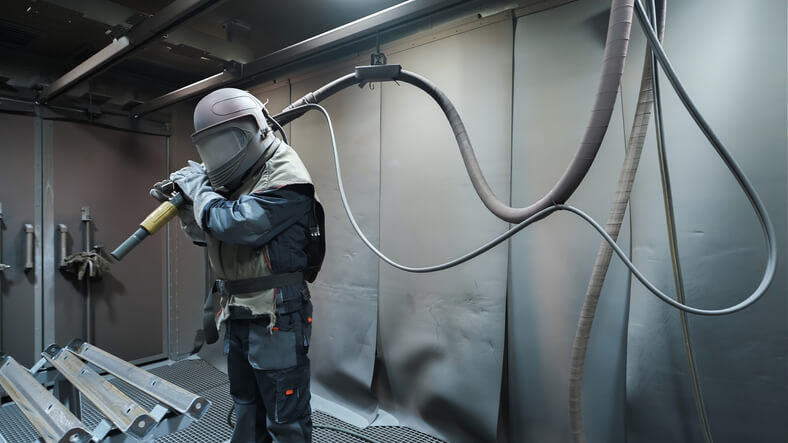
Metodi di sabbiatura fai da te
La sabbiatura dei metalli è un processo che può essere eseguito autonomamente da chiunque desideri trattare le proprie superfici senza rivolgersi necessariamente a specialisti del settore, semplicemente munendosi di una speciale pistola per sabbiatura facilmente reperibile sul mercato.
Tuttavia, è fondamentale comprendere che il fai-da-te è consigliabile solo per lavorazioni di piccole dimensioni e di complessità limitata, e nel rispetto delle seguenti precauzioni.
Dispositivi di Protezione Individuali (DPI) e Precauzioni
Prima di procedere con la sabbiatura, è essenziale adottare adeguate precauzioni e indossare i dispositivi di protezione individuali (DPI) appropriati:
- Maschere o sistemi di protezione delle vie respiratorie e degli occhi con alimentazione di aria dall’esterno per evitare l’inalazione delle polveri abrasive generatesi durante il processo.
- Occhiali protettivi sigillati per prevenire l’ingresso della polvere negli occhi.
- Guanti abrasivi adeguati per proteggere le mani dalle polveri abrasive.
- Scarpe di sicurezza con suola imperforabile per proteggere i piedi.
Alcune precauzioni aggiuntive che suggeriamo di osservare sono relative alle polveri prodotte, soprattutto se di alluminio perché a rischio esplosione.
Infine, ci teniamo a ricordare l’importanza di un corretto smaltimento delle polveri abrasive utilizzate. Dopo un certo numero di cicli, queste polveri, miscelate con i residui rimossi, devono essere smaltite attraverso imprese autorizzate.