La fresatura: cos’è e come avviene, processo e macchinari
Proprio come lo scalpello con un blocco di marmo, anche i metalli vanno incontro a lavorazioni meccaniche di sottrazione per trasformarsi in prodotto finito.
In questo articolo approfondiamo la lavorazione della fresatura, una tecnica che combina precisione ed efficienza per ottenere ogni forma desiderata.
Scorri per leggere:
- Cos’è la fresatura
- Il processo di fresatura: le 3 fasi
- La macchina fresatrice: componenti, tipologie e guida alla scelta
- Parametri meccanici da conoscere
- Quali differenze ci sono tra fresatura e tornitura?
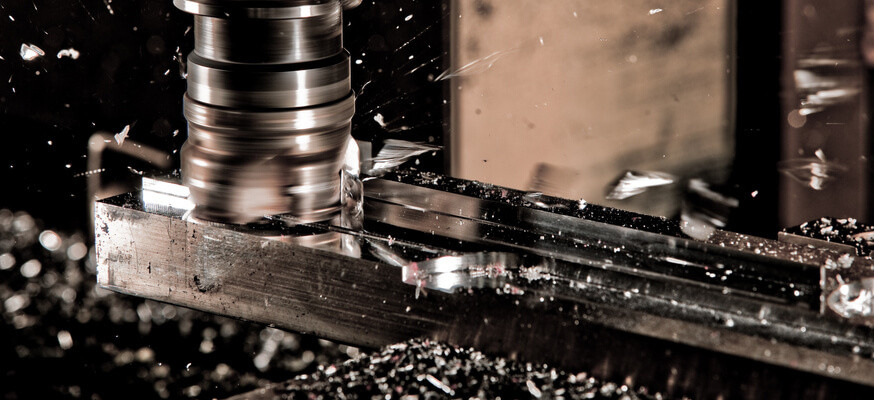
Fresatura: cos’è
La fresatura è una lavorazione meccanica che funziona per sottrazione, o asportazione, di materiale, utilizzata per produrre varie superfici (come piani, scanalature, spallamenti e forature) mediante l’uso di un utensile tagliente a geometria definita e con moto rotatorio.
Si effettua con frese montate su macchine utensili come fresatrici o fresalesatrici, dove l’utensile ruota e il pezzo trasla, permettendo ai taglienti della fresa di asportare metallo.
Il processo tipicamente comprende una fase iniziale di sgrossatura, che rimuove rapidamente grandi quantità di materiale, seguita da una fase di finitura, che invece asporta meno metallo per raggiungere dimensioni precise e una superficie liscia.
In parole semplici, per mezzo di una punta rotante è possibile tagliare e modellare materiali come metallo o legno.
Il pezzo viene fissato su una macchina detta fresa, la fresa ruota ad alta velocità e, muovendo il pezzo verso la fresa, si rimuove il materiale prima rapidamente per dare una forma approssimativa e poi più lentamente per ottenere la forma e la superficie finali desiderate.

Si tratta di una tecnica che presenta numerosi vantaggi tra cui l’elevata precisione e la qualità della finitura superficiale del prodotto finito, con la possibilità di raggiungere tolleranze inferiori al micron e superfici a specchio.
La fresatura può essere applicata a diversi materiali, utilizzando utensili che possono essere mobili, robotizzati o fissati su un telaio.
Gli utensili si dividono in frese integrali o frese ad inserti; queste ultime, più economiche, hanno inserti di metallo duro sostituibili una volta consumati.
Nel corso di questo articolo approfondiamo i concetti chiave di questa lavorazione che includono la velocità di taglio e l’avanzamento, che a loro volta determinano la velocità di rotazione dell’utensile e il movimento del pezzo.
Le 3 fasi del processo di fresatura
Ma come avviene il processo di fresatura di un metallo?
Abbiamo compreso che, proprio come un trapano, una testa tagliente e in rotazione, asporta trucioli di materiale fino ad ottenere la forma desiderata. Ma come?
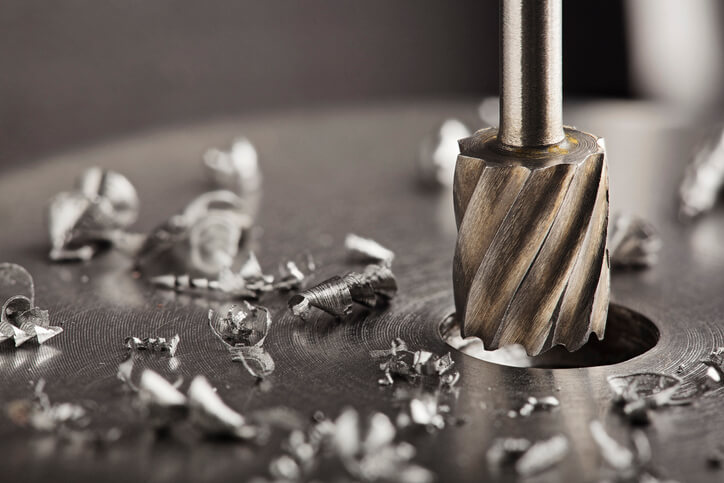
Il processo di fresatura si articola in diverse fasi cruciali, ciascuna con uno scopo specifico per ottenere risultati di precisione e qualità superficiale, ecco le principali:
Sgrossatura: Questa è la fase iniziale dove si rimuove rapidamente il materiale in eccesso dal pezzo grezzo. Utilizzando frese robuste e potenti, si mira a ridurre volumi significativi di materiale in modo efficiente ed economico. Questo sovrametallo lasciato dopo la sgrossatura fornisce la base per le fasi successive, garantendo margine per l’operazione di finitura.
Semifinitura: in questa fase intermedia, si procede con una rimozione più controllata del materiale per avvicinarsi alle dimensioni finali del pezzo. Vengono utilizzate frese più precise per ottenere superfici più lisce e preparare il pezzo per la fase finale di finitura.
Finitura: Dopo la sgrossatura, segue la fase di finitura che mira a raggiungere le dimensioni finali e a ottenere una superficie liscia e precisa. Qui si utilizzano frese più precise e controllate per rimuovere una quantità minore di materiale, rispettando le tolleranze dimensionali e il grado di rugosità specificato nel disegno tecnico. Questa fase è critica per garantire che il pezzo lavorato soddisfi esattamente le specifiche richieste.
Talvolta è richiesta la superfinitura, spesso eseguita usando metodi di lavorazione ad alta velocità.
Ogni fase del processo di fresatura richiede una pianificazione accurata e l’utilizzo di strumenti e frese specificamente progettati per ottenere risultati ottimali. La fresatura non è solo una questione di rimozione di materiale, ma anche di rispetto delle tolleranze dimensionali e della qualità superficiale, fondamentali per il successo del pezzo finito.
Tutte le tipologie di fresatura
Spianatura: utilizzata per rimuovere il materiale in eccesso da superfici piane, questa operazione è eseguita con frese apposite che garantiscono una superficie piatta e uniforme.
Contornatura o fresatura a spallamento: consiste nella creazione simultanea di due facce ad angolo retto tra loro. Questa tecnica è ideale per lavorare superfici che richiedono una transizione netta tra due piani, utilizzando frese apposite per ottenere risultati precisi e uniformi.
Copiatura o Profilatura: questa operazione è utilizzata per fresare forme complesse concave o convesse su più assi. È possibile utilizzare inserti specializzati per adattare la fresatrice alle forme specifiche richieste dal progetto.
Fresatura ad alto avanzamento: Caratterizzata da velocità di avanzamento elevate, questa operazione permette di ottenere una lavorazione rapida e efficiente grazie all’impiego di frese con angoli di taglio ottimizzati per una rimozione veloce del materiale.
A disco e per cave: Utilizzata per lavorare cave lunghe, profonde e aperte, questa tecnica sfrutta frese a disco laterale che permettono di gestire grandi volumi di materiale in modo stabile e produttivo.
Fresatura di smussi: Utilizzata per creare smussi e per eliminare spigoli vivi e bave dalle superfici lavorate. Questa operazione è essenziale per preparare le superfici per saldature o per migliorare l’estetica e la sicurezza del pezzo.
Fresatura a candela: preferita per lavorare cave corte e poco profonde, come scanalature e tasche chiuse, e per fresare sedi per chiavetta. Le frese a candela sono l’ideale per fresare forme complesse che non possono essere realizzate con altri tipi di utensili, garantendo precisione e versatilità in diversi contesti di fresatura.
La macchina fresatrice: componenti e funzionamento
La fresatrice è la macchina utensile impiegata nella lavorazione di fresatura.
Nella sua forma standard, si compone di tre elementi indispensabili che sono: il basamento, il motore e la fresa rotante.
Il basamento funge da supporto principale, sulla quale è posizionata la tavola dove il pezzo da lavorare è fissato. Un montante sostiene il mandrino, il quale, alimentato da un motore elettrico, imprime alla fresa il movimento rotatorio necessario per asportare il materiale.
La fresa stessa è l’utensile chiave installato sulla fresatrice per rimuovere il materiale in eccesso. Si tratta di un cilindro con denti taglienti lungo la sua circonferenza esterna, con lo spazio tra i denti, chiamato passo, che influenza la velocità e l’efficienza della fresatura. Le frese variano in base al numero e alla disposizione dei denti, determinando la qualità della finitura superficiale del pezzo lavorato.
Le fresatrici possono essere classificate in due categorie principali in base all’orientamento dell’utensile: fresatrici orizzontali e fresatrici verticali. Le prime presentano il mandrino montato orizzontalmente, mentre le seconde hanno la fresa orientata verticalmente, offrendo così diverse modalità di operazione a seconda delle esigenze di fresatura.
Nel contesto delle lavorazioni di meccanica di precisione, la fresatrice è indispensabile per la sua capacità di eseguire una vasta gamma di operazioni con un’unica configurazione di lavoro. Queste operazioni includono la rettifica, il taglio e l’alesatura, offrendo versatilità e precisione in diversi contesti industriali.
Le fresatrici professionali devono garantire due caratteristiche fondamentali: la capacità di muoversi su tutta la superficie del pezzo con precisione e la robustezza necessaria per assorbire le vibrazioni generate durante il processo senza compromettere la qualità del lavoro. Questi requisiti sono essenziali per garantire risultati precisi e uniformi nelle lavorazioni meccaniche avanzate.
Tutte le tipologie di macchine fresatrici
Esistono diverse tipologia di macchine fresatrici, a seconda delle lavorazioni da effettuare e dunque, dalla geometria della testa rotante.
Frese elicoidali: queste frese hanno denti elicoidali disposti lungo la loro superficie, ideali per la fresatura di superfici curve o per generare filetti su pezzi lavorati.
A denti sfalsati: caratterizzate da denti con posizioni sfalsate lungo la circonferenza, queste frese riducono le vibrazioni durante la fresatura, migliorando la qualità del taglio su materiali difficili.
Ad angolo doppio: con taglienti su entrambi i lati della fresa, queste sono adatte per operazioni di fresatura in due direzioni, ottimizzando l’efficienza e riducendo i tempi di lavorazione.
Frese piane: utilizzate per spianare superfici piane, queste frese sono dotate di denti posti in linea retta o leggermente inclinati, assicurando una superficie liscia e uniforme.
A candela: queste frese hanno una forma allungata e sottile, ideali per fresature in cavità profonde e strette, come scanalature e tasche chiuse.
A smussare: usate per creare smussi su spigoli vivi o per eliminare bave, queste frese sono progettate per migliorare la sicurezza e l’aspetto estetico dei pezzi lavorati.
Frontali: caratterizzate da taglienti posti sul fronte della fresa anziché lungo la circonferenza, queste sono utilizzate per fresature di precisione su superfici verticali o piane, consentendo un accesso diretto alla superficie da lavorare.

Fresatrici CNC: macchine a controllo numerico
Negli ultimi anni, moderni macchinari con tecnologia avanzata permettono di effettuare lavorazioni con elevata precisione e ripetibilità, lavorando in modo automatizzato ed eseguendo in autonomia le istruzioni fornite dal personale tecnico.
Si chiamano fresatrici CNC (Computer Numerical Control), macchine dotate di un sistema informatico che controlla il movimento degli utensili basandosi su istruzioni preimpostate, chiamate codici G o codici NC.
Questi codici definiscono la geometria del pezzo e il percorso dell’utensile, trasformando la lavorazione in una sequenza di punti facilmente interpretabili dal calcolatore.
L’operatore comunica al macchinario le specifiche del prodotto da realizzare, monitora il processo per garantire l’assenza di guasti o malfunzionamenti, e interviene se necessario.
Nella fresatura CNC, l’operatore inserisce le istruzioni nel computer che gestisce la macchina. Il sistema CNC interpreta queste istruzioni e guida l’utensile lungo il percorso definito. Durante il processo, l’operatore supervisiona la macchina, garantendo che funzioni correttamente e intervenendo solo in caso di problemi. Questo approccio automatizzato riduce significativamente il tempo di lavoro e i costi, migliorando al contempo la produttività e la precisione, con un margine di errore prossimo allo zero.
Vantaggi delle Fresatrici CNC
Le fresatrici CNC offrono numerosi vantaggi, tra cui:
- Riduzione del tempo di lavoro: la velocità e l’automazione del processo riducono i tempi di produzione.
- Diminuzione dei costi: l’efficienza del processo comporta una riduzione dei costi operativi.
- Alta precisione: la capacità di eseguire lavorazioni con una precisione fino a un micron (un millesimo di millimetro).
- Ripetibilità: la macchina può ripetere lo stesso processo con estrema precisione, garantendo la consistenza del prodotto finale.
Fresatrici CNC a 3 e 5 Assi
Le fresatrici CNC a 3 assi sono tradizionalmente utilizzate per ottenere lavorazioni con alta precisione. Tuttavia, i centri di lavoro CNC possono avere più assi di movimento, permettendo lavorazioni ancora più complesse. Queste macchine possono inclinare il mandrino su uno o più assi rotativi, o combinare un asse di rotazione del mandrino con un asse di inclinazione della tavola. Questa flessibilità consente di lavorare geometrie molto complesse, rendendo possibile la produzione di componenti intricati con un alto grado di precisione.
I parametri meccanici da conoscere
Ogni processo di fresatura richiede la precisa regolazione di diversi parametri cruciali per garantire la qualità del prodotto finale senza rinunciare all’efficienza del processo stesso.
Tra i principali parametri di lavoro della fresatura vi sono la velocità di taglio, la velocità di rotazione della fresa e l’avanzamento del pezzo.
Velocità di Taglio
La velocità di taglio (vc) è la velocità relativa tra la superficie da lavorare e l’utensile durante il taglio, espressa in metri al minuto (m/min). Questo parametro dipende dal materiale della fresa (o degli inserti dei taglienti) e dalla durezza del materiale da lavorare. Ad esempio, per lavorare acciaio dolce con una fresa in Widia, la velocità di taglio può arrivare a 140 m/min, e fino a 200 m/min se la fresa è dotata di ricoperture come il nitruro di titanio. Materiali più duri richiedono velocità di taglio inferiori.
Velocità di Rotazione
La velocità di rotazione della fresa (n) è il numero di giri che la fresa compie al minuto, ed è calcolata dividendo la velocità di taglio (vc) moltiplicata per 1000 per la circonferenza della fresa (il prodotto del diametro Ø per π). La formula è: n = Vc⋅1000 / π⋅D
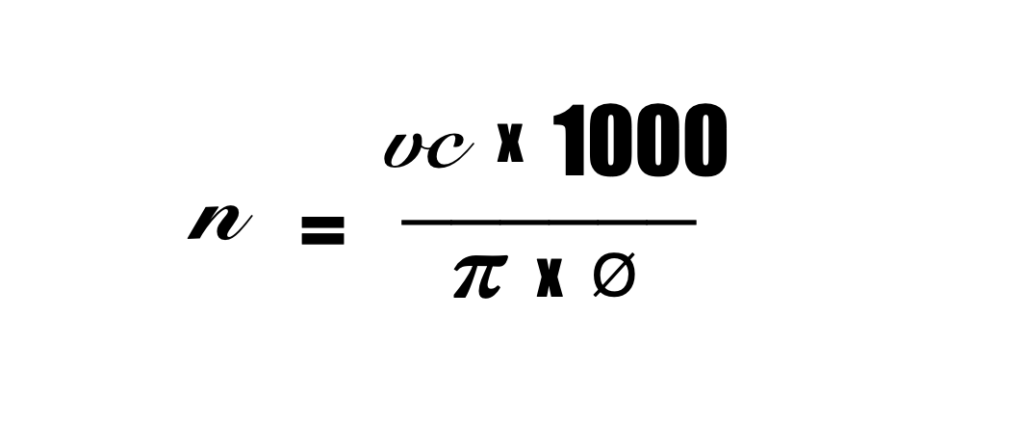
Avanzamento
L’avanzamento (vf) è la distanza che la fresa (o il pezzo) percorre durante ogni singola rotazione dell’utensile. Si calcola moltiplicando il numero di taglienti (z) per l’avanzamento per singolo tagliente (fz), e per la velocità di rotazione della fresa (n): vf=n⋅fz⋅z

L’avanzamento per singolo tagliente è stabilito da tabelle fornite dai produttori di utensili ed è espresso in micron o in centesimi di millimetro. Può essere aumentato per taglienti con geometria di taglio inferiore ai 90°.
Profondità di Taglio Assiale
La profondità di taglio assiale indica la profondità di lavoro della fresa nel pezzo lungo il proprio asse. Maggiore è la profondità, minore deve essere la velocità di avanzamento per evitare danni all’utensile o al pezzo. Per tagli profondi, è spesso necessario eseguire più passaggi.
Profondità di Taglio Radiale
La profondità di taglio radiale misura la profondità dell’utensile nella superficie in lavorazione lungo il raggio. Anche in questo caso, profondità elevate richiedono basse velocità di avanzamento e solitamente più passaggi per completare il lavoro.
Simbologia ISO dei Parametri di Fresatura
- vc: Velocità di taglio (m/min)
- z: Numero dei denti
- n: Velocità di rotazione (giri/min)
- fz: Avanzamento al dente (mm/dente × giro)
- fn: Avanzamento al giro (fz × z – mm/giro)
- vf: Avanzamento al minuto (fz × z × n; oppure fn × n – mm/min)
Scelta del materiale e influenza sui parametri
La scelta corretta di ulteriori componenti meccaniche può ottimizzare la produttività e ridurre al minimo gli errori. Ecco una panoramica di come diversi fattori interagiscono con i parametri di fresatura:
- Materiale della fresa: l’efficienza del taglio è influenzata dal materiale della fresa e dalla presenza di rivestimenti che ne migliorano le prestazioni. Frese in Widia o con rivestimenti in nitruro di titanio offrono velocità di taglio superiori.
- Densità dei taglienti: la densità dei taglienti dipende dal materiale da lavorare. Per esempio, l’alluminio richiede una bassa densità di taglienti per permettere lo scarico dei trucioli lunghi, mentre la ghisa, che produce trucioli in forma di polvere, può avere una maggiore densità.
- Tipo di truciolo: il tipo di truciolo prodotto influisce sulla scelta dei parametri di lavoro. Trucioli lunghi e aggrovigliati richiedono adattamenti specifici per evitare inceppamenti e assicurare un’operazione fluida.

Scelta degli utensili: fattori da considerare
La scelta della fresa corretta è strettamente legata alle caratteristiche degli inserti da combinare con il corpo fresa per ottenere risultati ottimali. Gli inserti, con le loro diverse dimensioni e forme, giocano un ruolo cruciale nella determinazione delle capacità di lavorazione.
- Dimensione e forma: la profondità di asportazione massima dipende dal numero di taglienti dell’inserto e dall’angolo di registrazione del tagliente.
- Tipologia: gli inserti possono essere monolaterali o bilaterali. Gli inserti bilaterali, avendo il doppio dei taglienti, offrono una soluzione più economica per ogni tagliente.
- Design specifici: inserti come il “wiper” (raschiante) garantiscono una finitura elevata in spianatura, mentre quelli ad alto avanzamento riducono lo spessore del truciolo e permettono avanzamenti più rapidi.
Scelta della fresatrice: fattori da considerare
Per selezionare la fresa ideale, è essenziale considerare vari elementi tecnici:
- Angolo di registrazione del tagliente (KAPR): influenza direttamente l’avanzamento al dente, la dimensione del tagliente e la profondità di taglio.
- Profondità di taglio massima (APMX): indica la massima profondità assiale che può essere raggiunta in una singola passata.
- Numero di denti della fresa (densità): rappresenta il numero di inserti per millimetro o pollice. Il passo della fresa, ovvero la distanza tra due inserti consecutivi, è cruciale per la lavorazione.
- Tipo di passo: può essere costante o differenziato. Un passo differenziato, con distanze variabili tra le sedi degli inserti, aiuta a ridurre le vibrazioni rispetto a un passo costante.
- Fori per il passaggio di refrigerante: alcuni corpi fresa sono dotati di fori interni per il passaggio del refrigerante, migliorando il raffreddamento dell’area di taglio e facilitando l’evacuazione del truciolo.
La combinazione di questi fattori permette di scegliere gli strumenti giusti per eseguire la fresatura in modo efficace, ottimizzando sia le prestazioni che i costi.
Quali differenze ci sono tra fresatura e tornitura?
Quando si parla di fresatura e tornitura nella produzione di guarnizioni e componenti industriali, spesso si genera confusione riguardo alle loro differenze.
Entrambe queste lavorazioni fanno parte del ciclo di lavorazione meccanica di precisione, ma hanno funzionamenti e approcci distinti che influenzano il modo in cui i materiali vengono lavorati.
Le lavorazioni meccaniche di precisione vengono eseguite utilizzando macchine e strumenti ad alte prestazioni, capaci di produrre forme e oggetti personalizzati per diverse industrie, dal settore industriale a quello medico.
Tornitura
La tornitura è un processo di lavorazione industriale utilizzato per creare rondelle, distanziali, guarnizioni industriali e altri articoli tecnici, principalmente da metalli. Questo processo avviene tramite l’asportazione del truciolo dal sovrametallo, modellando la superficie del pezzo.
Nel processo di tornitura, il pezzo di metallo viene fissato su un tornio che lo fa ruotare ad alta velocità. Mentre il pezzo ruota, un utensile tagliente si muove in modo controllato, incidendo e modellando il metallo per ottenere la forma e le dimensioni desiderate. È essenziale che il tornio sia stabile e il pezzo ben ancorato per garantire la precisione e la sicurezza durante la lavorazione.
Le fasi principali della tornitura sono due:
Sgrossatura: Rimozione iniziale di materiale in eccesso.
Finitura: Modellazione precisa del pezzo secondo le specifiche richieste.
Le operazioni principali che si possono eseguire con un tornio includono:
- Profilatura e troncatura: separazione di un pezzo dalla sua barra originale.
- Foratura: creazione di fori con l’uso di un trapano.
- Tornitura cilindrica: lavorazione interna ed esterna per ottenere il diametro desiderato.
- Tornitura tra spallamenti: creazione di scanalature ampie.
- Godranatura: creazione di righe su superfici cilindriche.
- Sfacciatura: aggiustamento delle dimensioni del pezzo.
- Filettatura: creazione di filettature su superfici cilindriche.
Fresatura
La fresatura, invece, è un processo in cui l’utensile rotante, chiamato fresa, si muove rispetto al pezzo di lavoro che rimane statico. La fresa rimuove materiale dal pezzo per creare la forma desiderata. Questo metodo è particolarmente adatto per lavorare superfici piane, scanalature e profili complessi.
Fresatura e Tornitura a confronto
La differenza principale tra fresatura e tornitura risiede nel movimento del materiale e dell’utensile:
Tornitura: il pezzo di lavoro è mobile e ruota mentre l’utensile tagliente si muove linearmente. Questo processo è ideale per lavorare pezzi cilindrici.
Fresatura: l’utensile rotante (fresa) si muove rispetto a un pezzo di lavoro statico. Questo metodo è adatto per creare superfici piane e forme complesse.
In sintesi, mentre la tornitura è utilizzata principalmente per pezzi cilindrici e per operazioni che richiedono la rotazione del materiale, la fresatura è ideale per lavorazioni su superfici piane e per creare forme complesse con un utensile in movimento. Queste differenze fondamentali nel funzionamento e nell’interazione tra utensile e materiale determinano l’applicazione specifica di ciascun processo nelle lavorazioni meccaniche di precisione.
Utilizzi e campi d’applicazione della fresatura
La fresatura è un processo versatile che trova impiego in una vasta gamma di situazioni e per numerose operazioni. Può essere utilizzata per la fresatura di estremità, la spianatura di superfici, e la creazione di smussi.
Oltre a queste applicazioni, la fresatura può sostituire operazioni come la foratura, l’alesatura, la svasatura e la filettatura per realizzare fori ciechi e passanti, filettature, cavità e una varietà di superfici complesse.
Si rivela ideale per la creazione di forme non simmetriche o che presentano elevate complessità, come fori, fessure, tasche, scanalature e profili tridimensionali.
Queste caratteristiche rendono il processo particolarmente adatto per la produzione di lotti limitati, prototipi e componenti progettati su misura. Inoltre, la fresatura è ampiamente utilizzata per la fabbricazione di utensili impiegati in altri processi, come stampi tridimensionali.
Grazie alla sua precisione, la fresatura può essere impiegata come lavorazione secondaria su semilavorati ottenuti tramite altri processi. Ciò consente di aggiungere caratteristiche ad alta precisione su pezzi già lavorati, migliorando ulteriormente la qualità e le specifiche tecniche dei prodotti finali.
Trai settori in cui questa lavorazione trova maggiore impiego ci sono l’industria automobilistica, aerospaziale, medicale, elettronica, settore energetico, macchine utensili, industria degli stampi, architettura e design, settore navale, produzione di prototipi.